From changing raw materials and technology to investing in solar power and reducing carbon emissions, many businesses are proactively transforming themselves to affirm their position in the global supply chain.
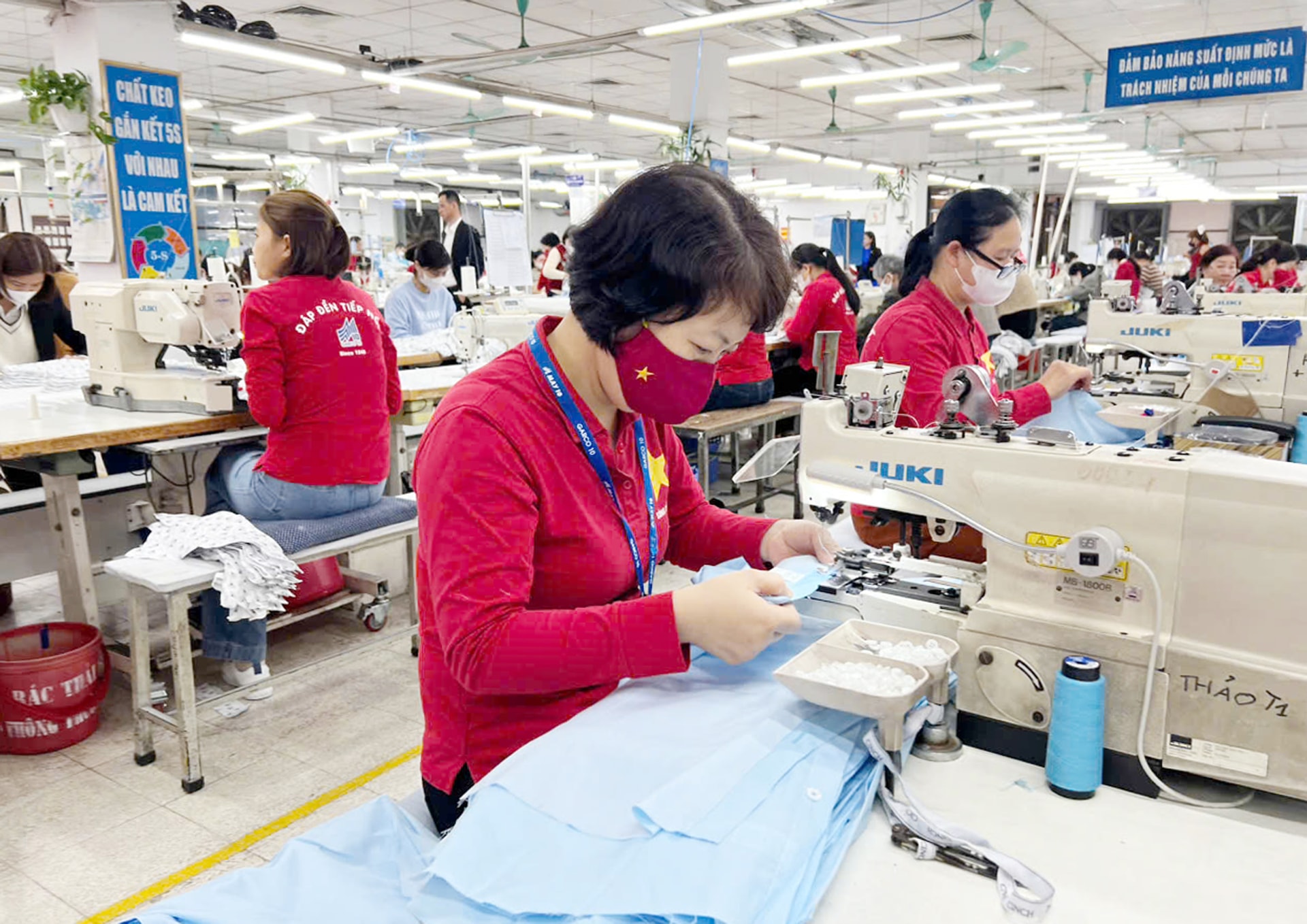
Green from raw materials to technology
Along with the increasingly high demands on the quality of exported textile products, in recent times, green production to meet sustainable development requirements has become the top criterion of major markets such as the United States, the European Union, Japan... In response to the strict requirements of the market, the textile industry has made efforts to keep up, invest in clean production technology, deploy green factory models, save resources, reduce emissions and carbon footprints, develop environmentally friendly products...
As one of the emerging enterprises in transforming sustainable production, General Director of May 10 Corporation - JSC (May 10) Than Duc Viet said that greening in production is no longer a matter of "wanting or not" but has become a "mandatory requirement". Grasping this trend, May 10 has implemented many solutions to promote green production, environmental protection associated with social responsibility, smart production... Typically, the enterprise has spent nearly 60 billion VND to implement the greening strategy and transform production.
"Previously, 100% of May 10's boilers used fossil fuels such as coal, but now we are gradually switching to using renewable energy. By the end of 2024, 90% of May 10's boilers will use renewable energy. This year, we will change all boiler combustion equipment to use renewable energy, aiming to reduce about 20,000 tons of carbon emissions into the environment," Mr. Than Duc Viet informed.
At May 10, "greening" production also means investing in modern machinery and equipment, aiming to cover the entire building block with rooftop solar power, providing clean electricity for production... Currently, the solar power system contributes 838kWp capacity at Bim Son Garment Factory, 999kWp at Hung Ha Veston Factory, 631kWp at Ha Quang Garment Factory. In addition to energy, May 10 is also a pioneer in developing circular fashion , using organic fabrics, and minimizing textile waste.
Similarly, Director of the Red River region, Song Hong Garment Joint Stock Company Nguyen Ngoc Khuyen informed that in order to move towards green production, the enterprise has worked with customers and suppliers early on, to research and exploit suitable raw and auxiliary materials, paying special attention to finding products of recycled origin. At the same time, during the process of building the factory, Song Hong Garment also prioritized the "green" factor, using and exploiting solar power sources, reducing the load on the national grid; using electric boilers instead of coal-fired boilers, minimizing environmental pollution.
The government needs to accompany businesses
Statistics show that the global sustainable fashion market is estimated at 7-8 billion USD/year and is expected to increase to 33.05 billion USD by 2030. Therefore, clean and sustainable production is the "lifeline" of textile and garment enterprises. However, green and sustainable production is a long process, requiring efforts from both enterprises and timely support from the Government.
According to Mr. Than Duc Viet, the “greening” of production poses many challenges for businesses. First of all, it is the awareness of emission reduction and circular economy . If they do not catch up, they will fall behind while businesses face many difficulties in human resources as well as financial resources to invest in greening...
"We define green production as not only investing in finance, factories, modern technology... but also investing in human resources, so training must be enhanced to be able to access the best technology" - Mr. Than Duc Viet stated.
Meanwhile, Chairman of the Vietnam Textile and Apparel Association Vu Duc Giang said that in order to develop sustainably, from now until 2030, the textile and garment industry will gradually shift from a focus on rapid development to sustainable development and circular business. In the period 2031 - 2035, the industry will develop effectively and sustainably according to the circular economic model; perfect the domestic value chain and participate in a high-value position in the global supply chain. Export and domestic consumption with private brands of regional and world stature.
The main solution of the industry is to continue investing in sustainable development, science and technology development and human resources. Notably, attracting high-tech weaving, dyeing and finishing projects to industrial parks; investing in the production of new raw materials of natural origin, environmentally friendly; digital transformation, investing in the development of the textile and garment fashion industry...
“Bringing circular products into the textile and garment sector is a must, so the Government needs to work with businesses to build a “greening strategy”, invest in factories with infrastructure that meets brand standards in terms of working environment, wastewater, emissions, renewable energy...” - Mr. Vu Duc Giang stated.
According to experts, currently 80% of the total 7,000 domestic textile and garment enterprises are small and medium-sized, with very limited capital for investment in modern technology, so there needs to be a fund to support green development enterprises, with interest rates of only 0 - 2%/year to encourage enterprises to comply with COP 26 commitments.
Source: https://hanoimoi.vn/nganh-det-may-viet-nam-xanh-hoa-de-khang-dinh-vi-the-708265.html
Comment (0)