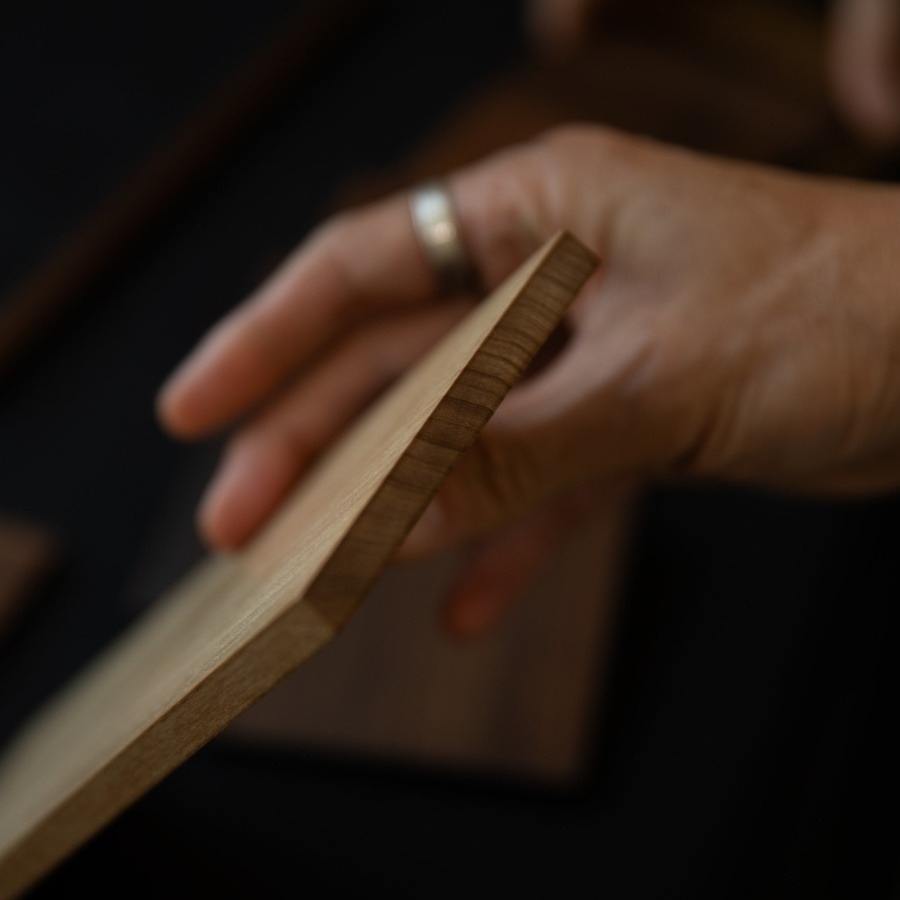
In the vast warehouse of a startup called InventWood, a strange new material will soon begin mass production: Softwood transformed at the molecular level into a material that is stronger than steel but six times lighter.
Superwood - the name of this special material, is expected to be able to replace steel beams in the skeleton of a building, and is also impact resistant enough to make bulletproof doors.
Additionally, the material is fire-resistant. The outer layer of Superwood will also carbonize in a way that protects the inside, preventing it from collapsing in a fire like steel.
Modified wood
Liangbing Hu can be considered the "inventor" of engineered wood. Before teaching at Yale, Hu was the director of the Center for Materials Innovation at the University of Maryland.
There, he invented a variety of unique woods that had properties such as being transparent, moldable like plastic, and bouncy like a rubber ball. All of Hu's inventions manipulate wood at the molecular level.
![]() |
Wood has a compact structure and is as durable as steel. Photo: InventWood. |
In 2018, Hu and his colleagues continued to make waves in the materials science world when they presented the technology behind Superwood in a paper in Nature.
To create the material, the team starts by cooking and chemically treating the wood. They then compressed it, making a typical board up to four times lighter. In the process, Hu discovered that the experiment pushed the cellulose fibers closer together, collapsing the channels that make up the tree's circulatory system.
At first, the experiment seemed like a remarkable discovery that would eventually remain in the gallery. Many people approached Hu about the business, but he told them that he was just a university professor and had no idea what to do with the project.
Instead of giving up, however, Hu spent the next few years refining the technology, reducing the material's production time from more than a week to just a few hours.
After the initial attention, most surprisingly considered Superwood a novelty. However, Alex Lau, CEO of InventWood, reached out to Hu and helped commercialize the company in 2021.
The startup later received a $20 million grant from the Department of Energy in 2022, and received an additional $30 million in financing from various investors.
Huge potential
The startup is now producing its first batches of Superwood, starting this summer. Lau says the first commercial plant of its kind is small. The initial products will be used to build the “skin” of a building, the non-load-bearing parts that still require aesthetics and durability.
![]() |
A sample of Superwood (darker wood) next to regular wood, undergoing a long-term weight-bearing bending test. Photo: Wall Street Journal. |
In the long term, they want to move towards replacing the backbone of the building from traditional materials to super-hardwood. “Ninety percent of the carbon emissions from buildings come from concrete and steel during construction,” said Mr. Wipe.
To build the plant, InventWood raised $15 million in its first Series A round. The round was led by the Grantham Fund, with participation from Baruch Future Ventures, Builders VC, and Muus Climate Partners, three prominent funds investing in sustainable technology, climate, and materials innovation.
Superwood starts with regular wood, which is mainly composed of two compounds: cellulose and lignin. In fact, nanocrystalline cellulose is actually stronger than carbon fiber. So the main goal is to enhance the strength of this inherent essence of wood.
The company uses chemicals used in the food industry to modify the molecular structure of wood, then compresses the material to increase the number of hydrogen bonds between cellulose molecules.
With the ability to compress material four times, many people would think Superwood is stronger by the same amount. “But it is actually about 10 times stronger due to the additional bonds created during this process,” Lau explains.
![]() |
When sandwiched between lighter-colored conventional wood, Superwood can strengthen load-bearing alternatives to steel beams in home framing. Photo: Wall Street Journal. |
The result is a material with a 50 percent higher breaking strength than steel and a strength-to-weight ratio 10 times better, the company says. It also meets Class A fire standards, meaning it is highly resistant to fire and is resistant to rot and insect damage.
In fact, whether or not to incorporate Superwood into structural elements in buildings still requires certification from the company's partners, including builders and architects. In addition, Superwood also requires new construction processes, as the material is strong enough to eliminate the typical steel joints in engineered wood structures.
The material's applications could also extend beyond construction, according to the WSJ. Superwood is like carbon fiber, but less brittle. It's already used in everything from sports equipment and tennis shoes to race cars and airplanes.
Source: https://znews.vn/sieu-vat-lieu-chong-dan-chong-chay-va-ben-hon-ca-thep-post1565040.html
Comment (0)